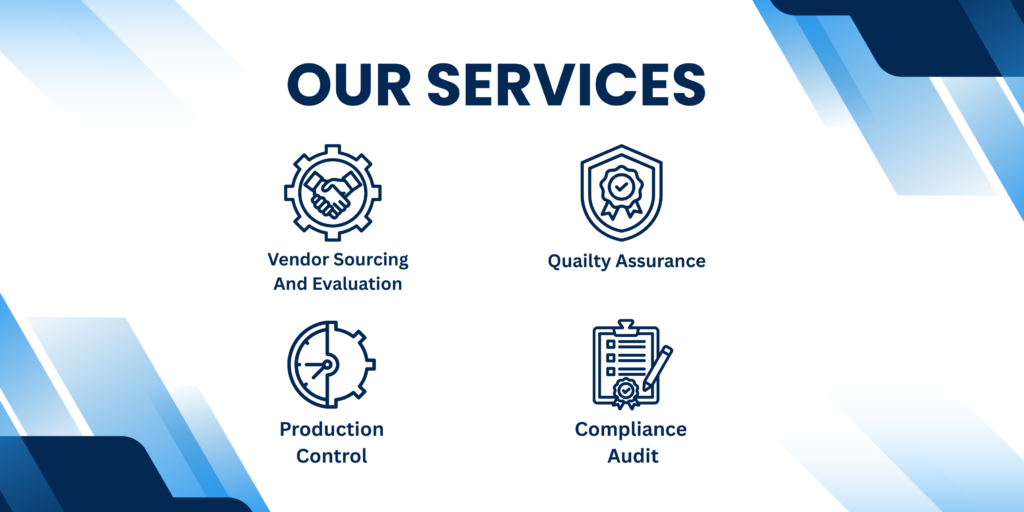
Vendor Sourcing and Evaluation
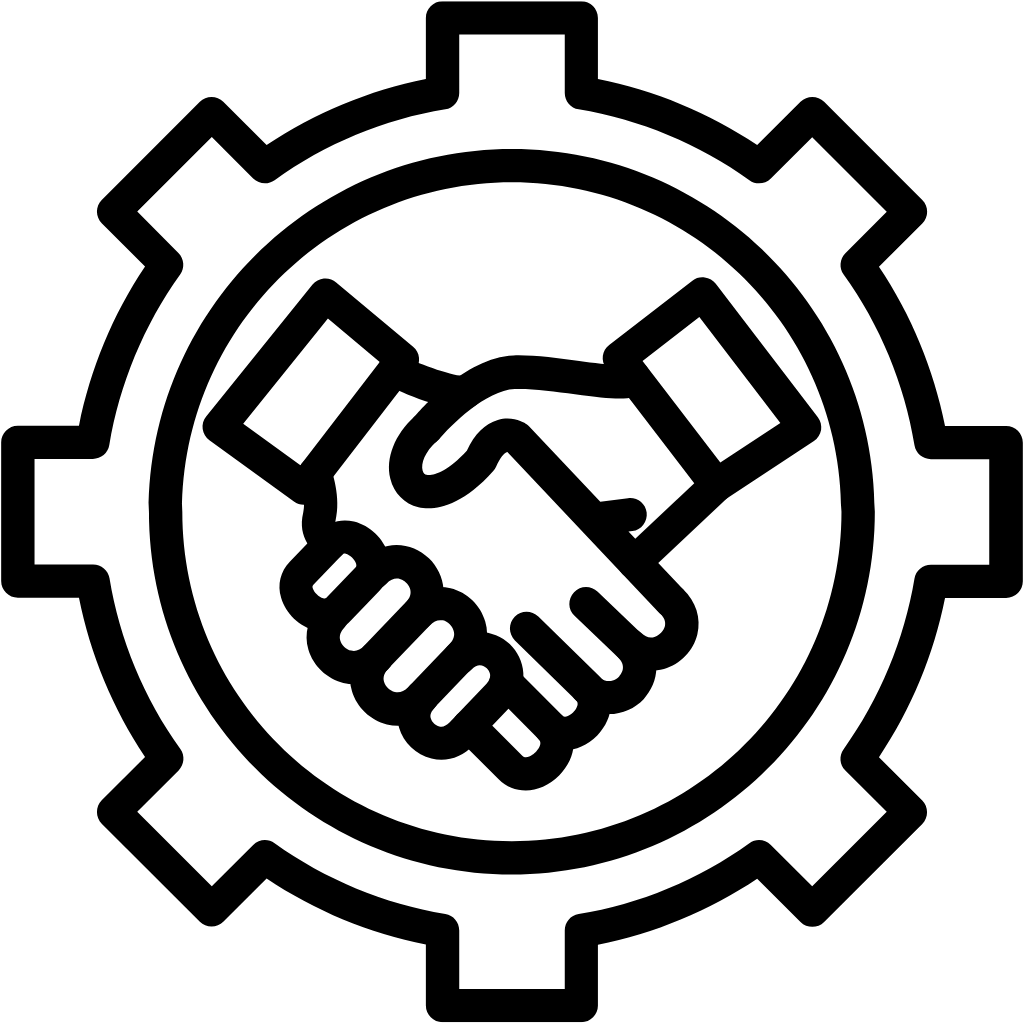
we specialize in identifying, evaluating, and partnering with reliable vendors to ensure our clients receive the highest quality products and services at the most competitive prices. Our vendor sourcing process is driven by in-depth market research, supplier benchmarking, and strategic alignment with our clients’ business goals.
We conduct a thorough evaluation of each potential vendor based on key criteria such as quality standards, compliance, production capacity, financial stability, lead times, and cost-effectiveness. Our team maintains a comprehensive supplier database and continuously monitors vendor performance to ensure long-term value and reliability.
With NS Sourcing, clients benefit from a streamlined sourcing process, improved supplier relationships, and reduced risk—ensuring optimal supply chain efficiency and success.
Quality Assurance
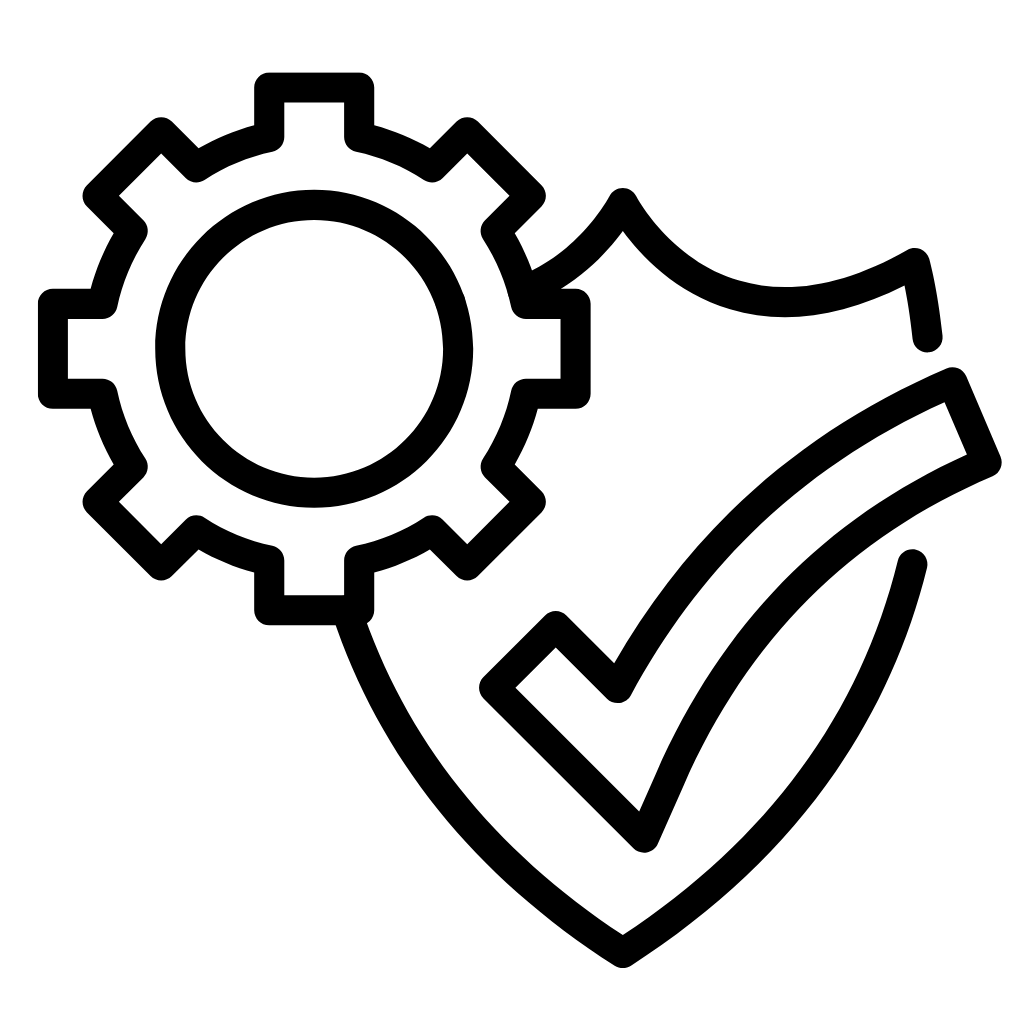
quality is at the core of everything we do. Our dedicated Quality Assurance team ensures that every product sourced meets the highest industry standards and client expectations. From initial sampling to final shipment, we implement rigorous quality control protocols at every stage of the production process.
We work closely with our suppliers to enforce strict compliance with international quality standards, conduct factory audits, and perform detailed inspections—including pre-production checks, in-line monitoring, and final product evaluations. Our proactive approach minimizes defects, reduces rework, and ensures consistent product excellence.
With NS Sourcing, clients can trust that quality is never compromised—every item delivered is a reflection of our commitment to reliability, precision, and customer satisfaction.
Production Control
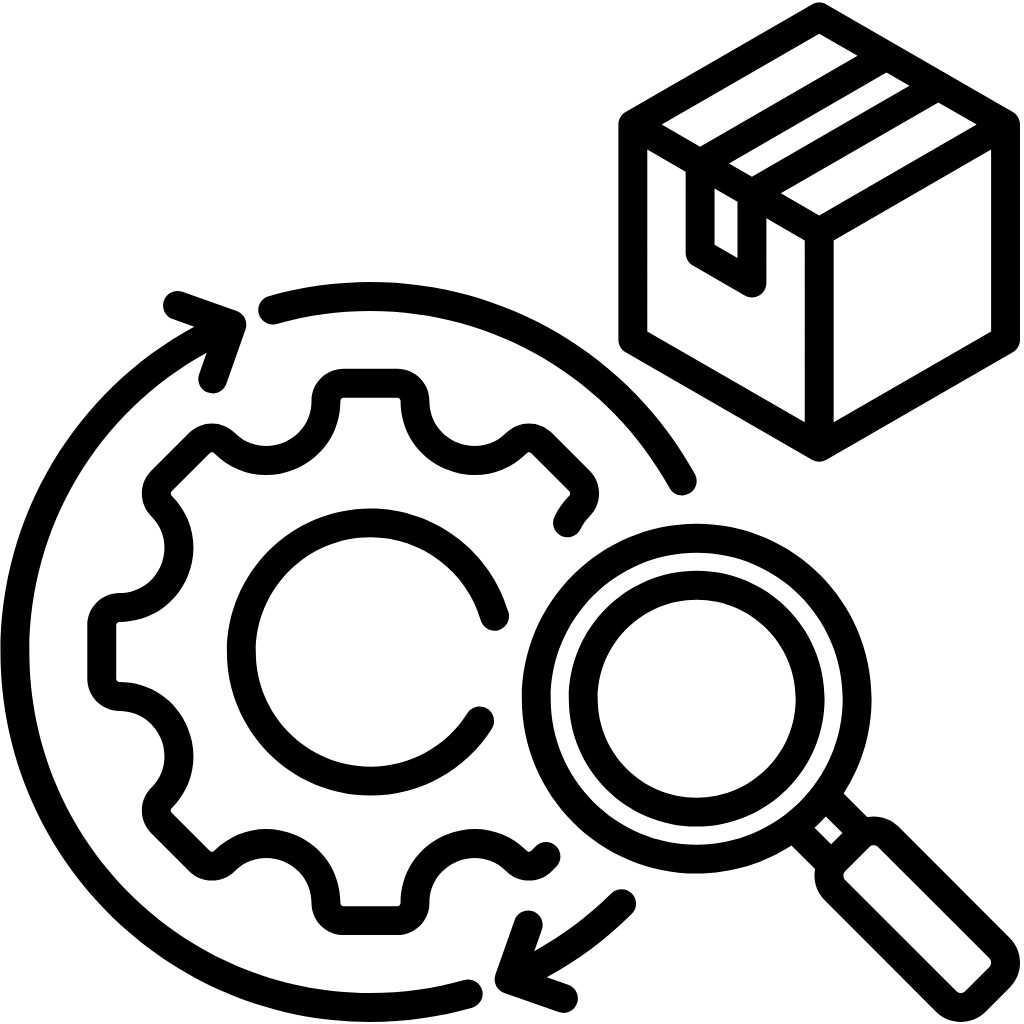
effective Production Control is key to delivering on time, on budget, and to specification. Our team ensures that every step of the production process is meticulously planned, monitored, and managed to maintain efficiency, consistency, and quality from start to finish.
We coordinate closely with manufacturers to set clear production timelines, track progress in real-time, and proactively address any delays or issues that may arise. Our approach includes detailed production planning, workflow optimization, capacity management, and continuous communication with suppliers to ensure alignment with client expectations.
With NS Sourcing overseeing production control, clients benefit from minimized lead times, reduced risk of disruption, and a smoother path from order to delivery—ensuring every project is executed with precision and professionalism.
Compliance Audit
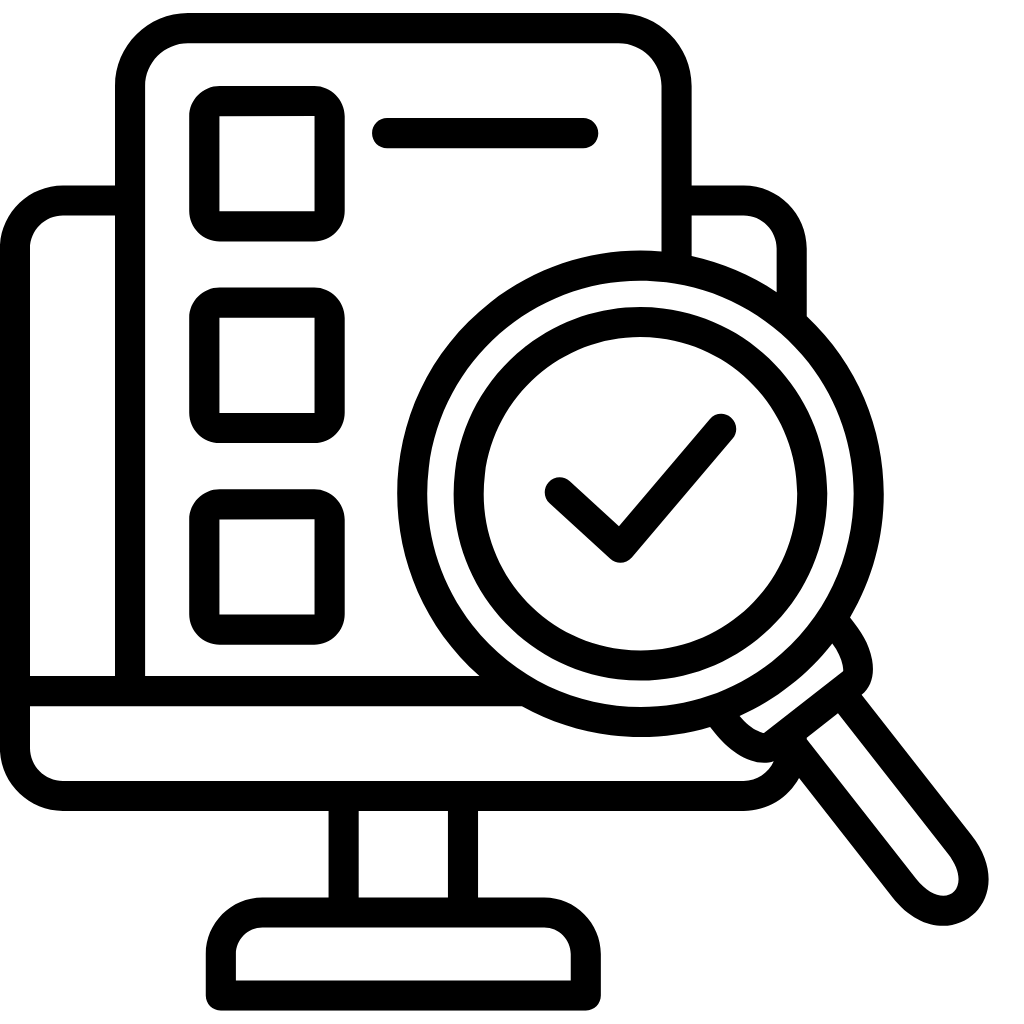
our Compliance Audit services are designed to ensure that every supplier and production partner adheres to international standards, local regulations, and our clients’ specific ethical and operational requirements. We conduct thorough audits across multiple areas, including labor practices, health and safety, environmental responsibility, and factory operations.
Our experienced audit team performs on-site assessments, document verification, and worker interviews to evaluate compliance with standards such as ISO, SA8000, WRAP, and BSCI. We provide detailed audit reports, risk assessments, and corrective action plans to help suppliers improve and maintain compliance.
With NS Sourcing, clients gain confidence in a transparent, responsible, and ethical supply chain—built on accountability, trust, and continuous improvement.